Porous Sintered Materials
In the world of filtration technology, PE sintered filters have emerged as a reliable and versatile solution for a variety of industrial applications. Knowing for their durability and efficiency, these filters are used in numerous industries, including automotive, chemical processing, food and beverage, and more.
Here delves into the composition, manufacturing process, applications, and benefits of PE sintered filters.
Hope to know us more. Pls click now.
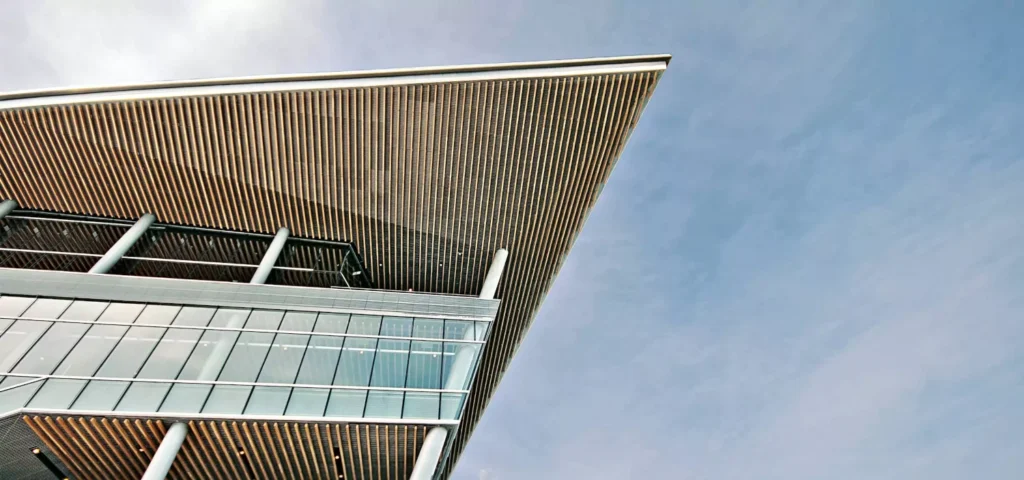
Our Product
We could provide customized product with your drawing attached.
There are some common size for your reference with required pore size.
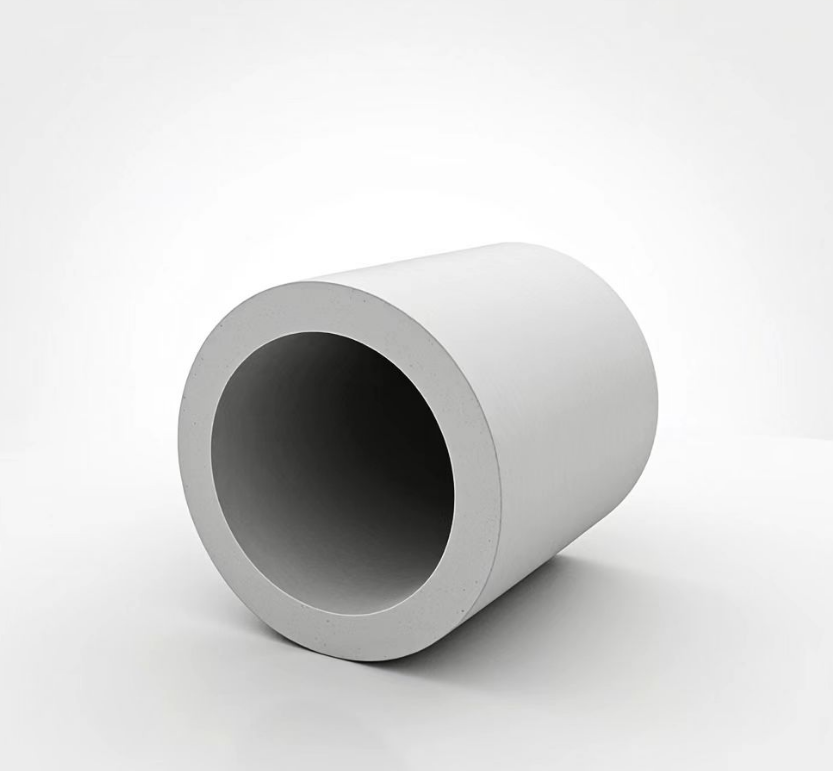
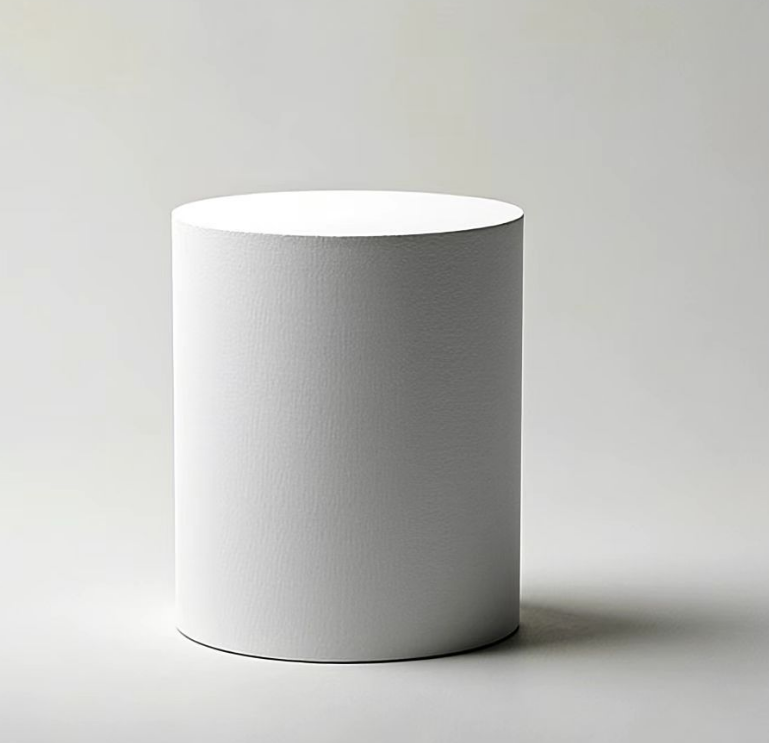
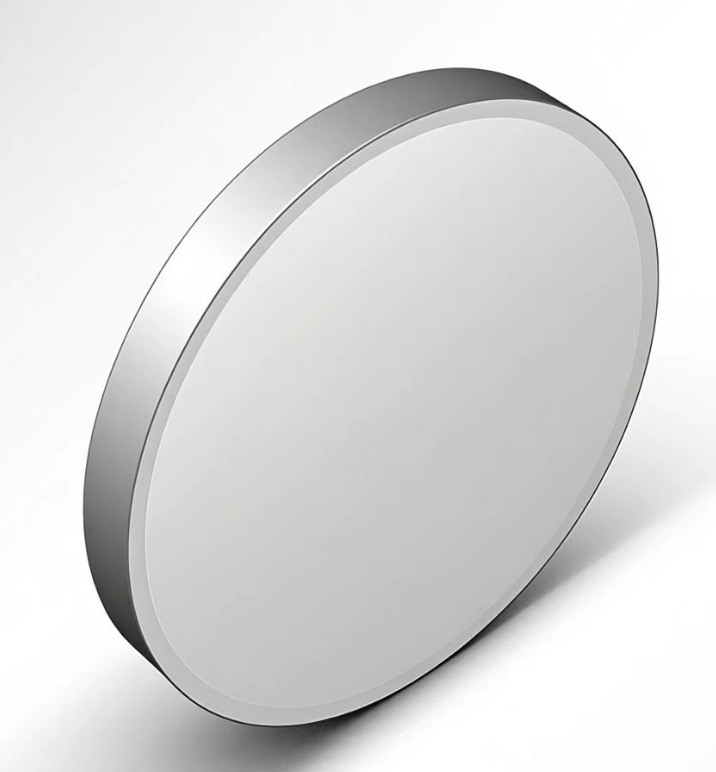
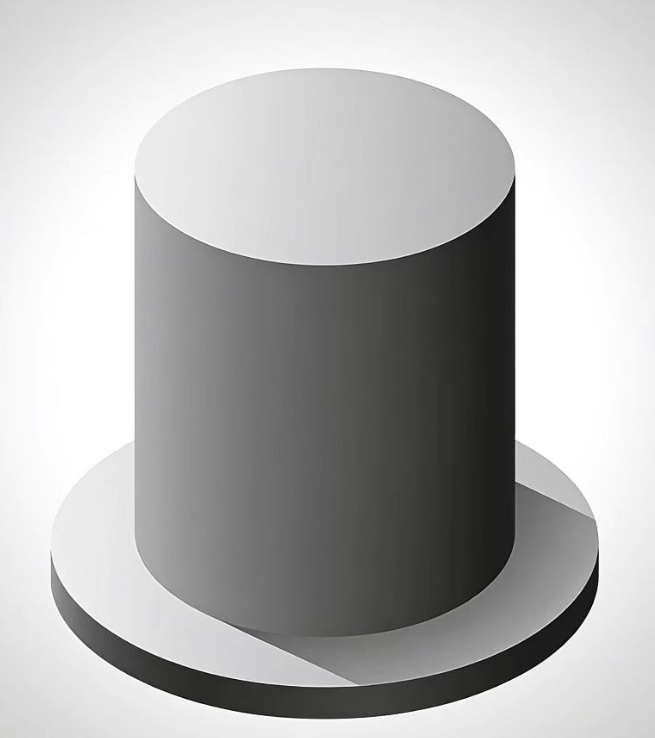
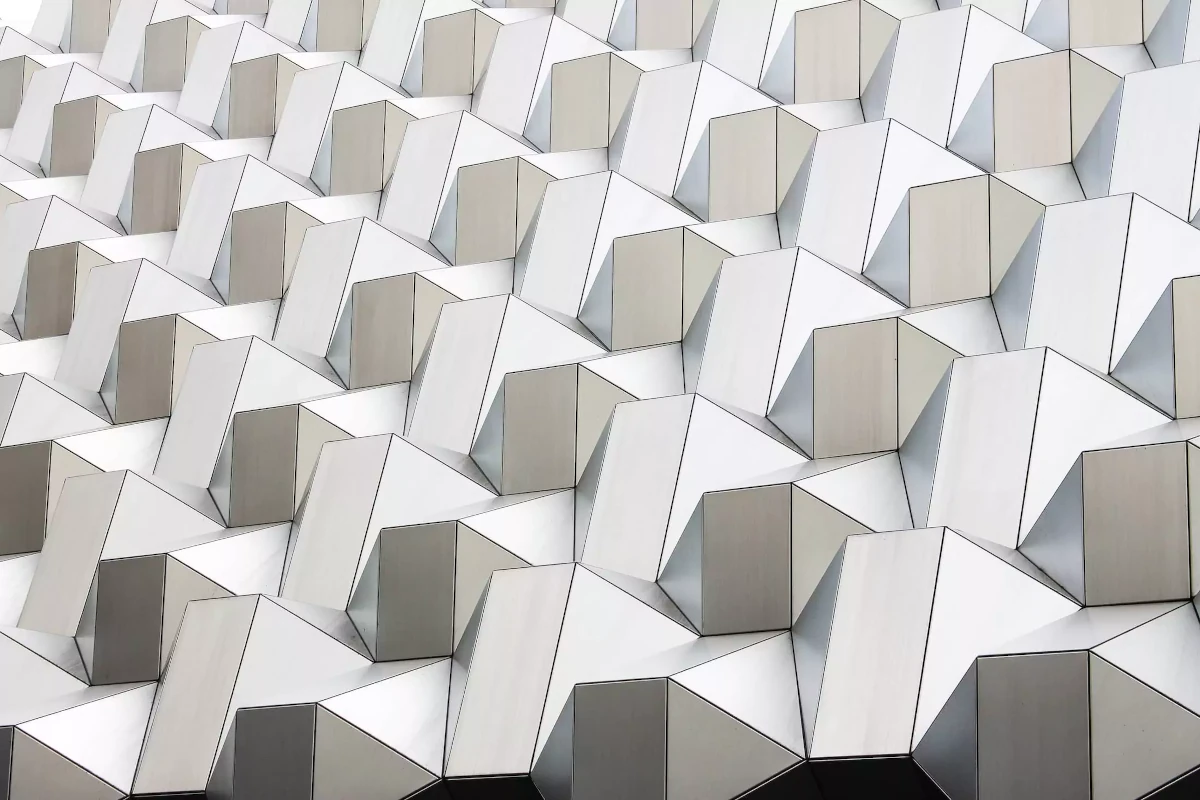
Typical Application
Suction canister
Infusion set
ESR test tube
Arterial blood collection device
Indwelling needle
Microfluidic chip
Manufacturing Process
The production of PE sintered filters involves several key steps:
- Powder Selection: High-quality polyethylene powder is chosen based on the desired filter properties.
- Molding: The powder is placed in a mold to form the desired shape and size of the filter.
- Sintering: The mold is heated to a temperature below the melting point of polyethylene, causing the particles to bond together.
- Cooling: After sintering, the filter is cooled to solidify its structure.
- Finishing: The filter may undergo additional processes such as cutting, drilling, or surface treatment to meet specific application requirements.
Q&A
What are PE Sintered Filters?
PE sintered filters are made from polyethylene (PE), a thermoplastic polymer. The sintering process involves compacting and heating the PE powder without melting it, resulting in a porous structure. Under the appropriate manufacturing technique, it has uniform pore size distribution, and the interior presents a porous maze like structure. This unique structure allows the filter to effectively trap particles while maintaining a high flow rate.
What is PE filter self-sealing function?
Most venting materials, such as membranes only have the function of blocking water and allowing air to pass through, and they have bidirectional exhaust. And with an obvious difference from other venting material, PE sintered materials can achieve the function as one-way valves while contacting with water.
What is the max & min diameter for PE filter?
Now we could provide the diameter from 10um to 20um.
Could PE filter achieving odor adsorption function?
We could provide activated carbon filter, which meet your requirement. Made by mixing activated carbon powder and PE material, it ensures particle retention and filtration while having odor adsorption. The adsorption rate of gases such as SO2, NH3, toluene can reach up to 70%, achieving both filtration and adsorption functions.
What is the raw material of porous sintered product?
Most customers commonly use High density polyethylene (HDPE) and ultra-high molecular weight polyethylene (UHMWPE) as sintering materials. In addition, they also use polypropylene (PP) and PP/PE as raw materials for sintered filtration materials.
HDPE is commonly used as a filter material for large pore sizes, while UHMWPE is commonly used as a filter material for small pore sizes below 20μm and porosity up to 60%.
Our advantage
- Customized
- Quick delivery
- Quick response
- Small MOQ
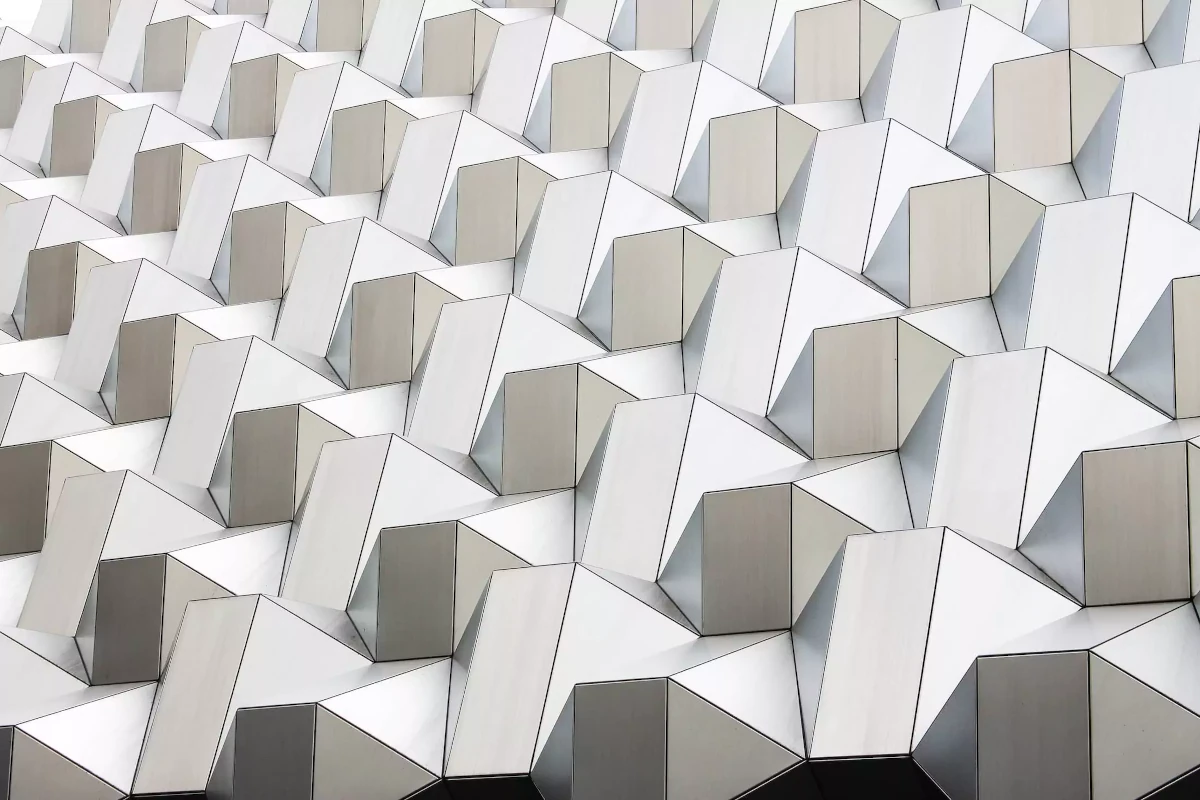
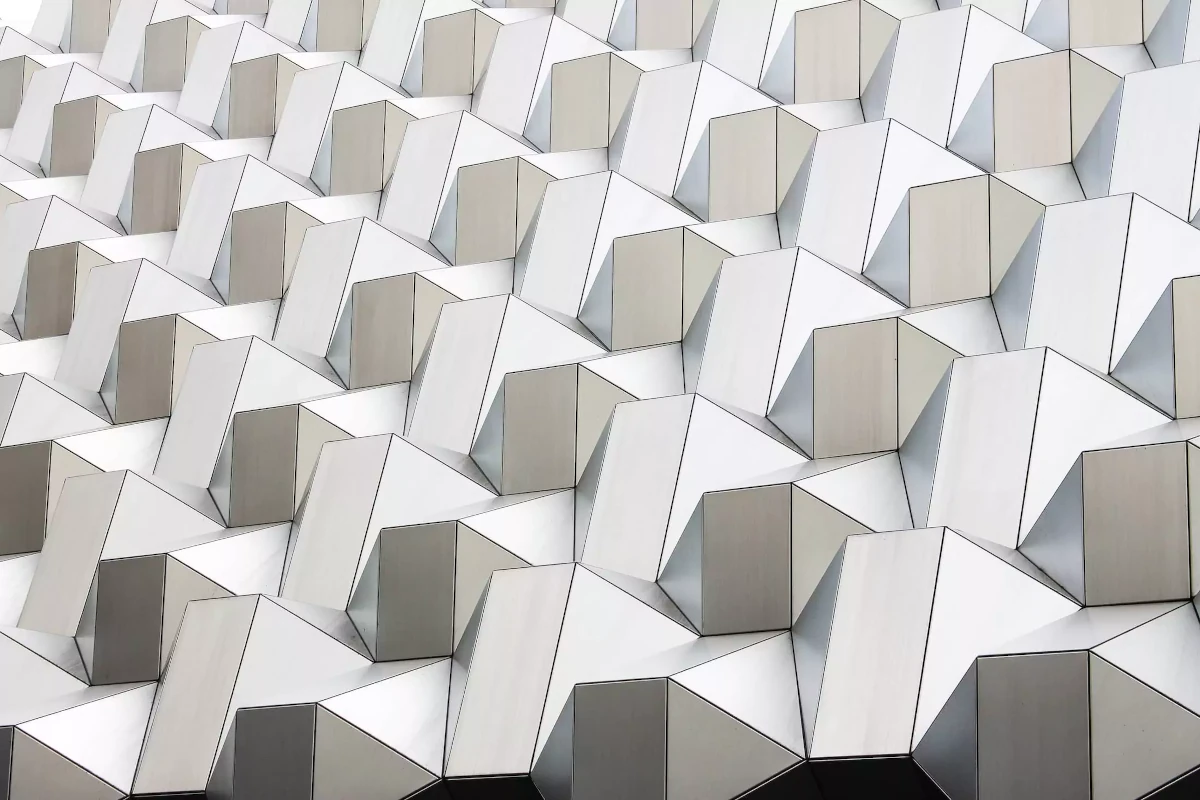
PE sintered filters provide a reliable and efficient solution for a wide range of filtration needs. Their unique properties, combined with a customizable design, make them an ideal choice for industries seeking high-performance filtration systems. As technology advances, the applications and capabilities of PE sintered filters are likely to expand, offering even greater benefits to industries worldwide.